Sponsored: Focus on Sustainable Manufacturing Positions Ross Video Factory for Net-Zero Carbon Future
By early next year, Ross will have reached its goal and advanced the cause of sustainability
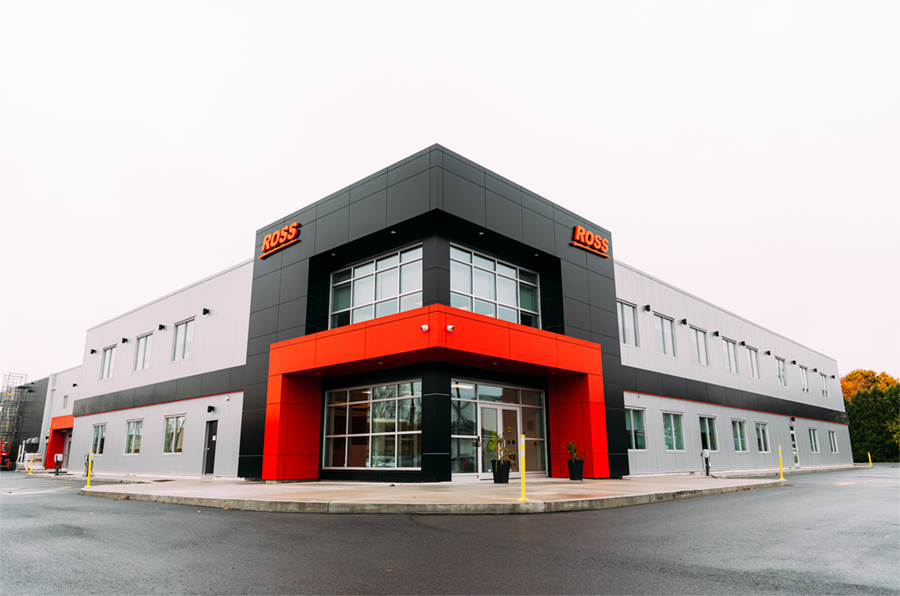
While most broadcasters and video professionals recognize Ross Video for its leadership in developing many of the key technologies used in the production of television as well as non-broadcast video, many may be surprised to learn that the company is also an industry leader in sustainable manufacturing.
Five years ago, Ross Video began a project to expand its factory in Iroquois, a small town in southeastern Ontario, Canada, near the banks of the St. Lawrence River, from the existing 65,000-square-foot manufacturing floor to 120,000 square feet.
One of the primary goals in designing the expansion was to advance the company’s environmental initiatives with the goal of achieving net-zero carbon emissions. As Ross Video’s chief manufacturing officer, I am pleased to report that the factory will reach that goal within the next few months.
Achieving this ambitious feat started more than a decade ago when Ross Video put in place measures to comply with the RoHS Directive restricting hazardous substances, such as metals like lead, mercury and cadmium and other substances.
While not specific to carbon neutrality, RoHS Directive compliance launched Ross Video on the road to sustainability. By 2008, the company was firmly on the way to establishing a culture of environmental consciousness. Ross established mandates to source locally, especially for larger, bulky goods, when possible.
The shorter the distance bulky items must move, the less the fuel used—and therefore the lower the carbon emission required to deliver those items to the factory. One of the bulkiest items required by the factory is packaging. When cardboard is shipped, it’s inevitable that a lot of air is shipped as well.
Working with these local sources, Ross co-designed the packaging to ensure it is fully up to industry standards with regards to shake and drop testing. Plus, the proximity of the sources to the factory translates into less carbon emitted in shipping.
The same is true of shipping machined metal—there’s a lot of air—and most importantly a lot of weight. The closer the source, the shorter the distance and, most importantly, the less fuel required, meaning a much smaller carbon footprint.
The company also took steps to eliminate generating wastewater and environmentally harmful air emissions from the factory. Ross also looked for ways to make more efficient use of power.
At about the same time in 2018, key European customers like BBC, Sky, ITV, IMG and others told Ross that future purchases would be contingent on two company executives attending a carbon literacy day in London. As one of those executives, I was pleased to learn that the instructor presenting the course thought Ross was in pretty good shape—perhaps the most advanced among the hardware vendors in the industry. However, there was still more to do.
Shortly after the literacy day, Ross began planning for its factory expansion. It was clear for quite some time that the real gains to be made in carbon footprint reduction centered on capital equipment investment.
To make the most of the opportunity to reduce carbon that the expansion presented, Ross hired Red Squirrel Environmental, a Kingson, Ontario, Canada, non-profit to conduct a Level 2 ASHRAE (American Society of Heating, Refrigerating and Air-Conditioning Engineers) audit to help the company identify where the factory was using power, find the source of emission and offer guidance with the goal of achieving a net-zero carbon footprint with the expanded factory. That information factored heavily into the factory design and put Ross on the path to its emissions goal, which will be achieved no later than Q1 2025.
A couple of other factors have played a big role in achieving this goal. First, the new factory expansion includes rooftop solar power generation. Interestingly, a 2012 expansion of the facility was scheduled for solar, but shortly after its completion local building codes aimed at improving seismic protection prevented the company from adding the weight of solar panels to the roof. However, the latest expansion cleared the way for solar power, which now plays an important role in reaching the net-zero carbon goal.
Second, Ross Video CEO and majority shareholder David Ross as well as his family are quite supportive of efforts to make the company’s manufacturing and entire operation more environmentally friendly.
In fact, Ross Video’s commitment to environmental protection and sustainability extends well beyond the company’s factory. The same emphasis on sustainability is factoring into product design—most notably the Ross Video Ultrix Hyperconverged production platform.
By combining many production functions previously only accessible from discrete production devices, Ultrix delivers substantial power, weight and cabling efficiencies—benefits that are particularly important in OB trucks when it comes to reducing carbon footprint.
Notably, Ross Production Services is walking the sustainability walk with its implementation of Ultrix in OB trucks and flypacks. The facilities provider has been building its production units based on Ultrix since its introduction.
As a result, it has been able to design and build a 16-camera 4K hyperconverged unit leveraging Ultrix in a 40-foot box truck chassis with the same production punch available in a traditional 53-foot production trailer.
As Ross Video moves forward, the company remains committed to implementing other measures to advance its sustainability goals even further. That’s good news to European broadcasters—and one day to broadcasters worldwide—as they continue to look for ways to advance their own sustainability efforts.
Get the TV Tech Newsletter
The professional video industry's #1 source for news, trends and product and tech information. Sign up below.
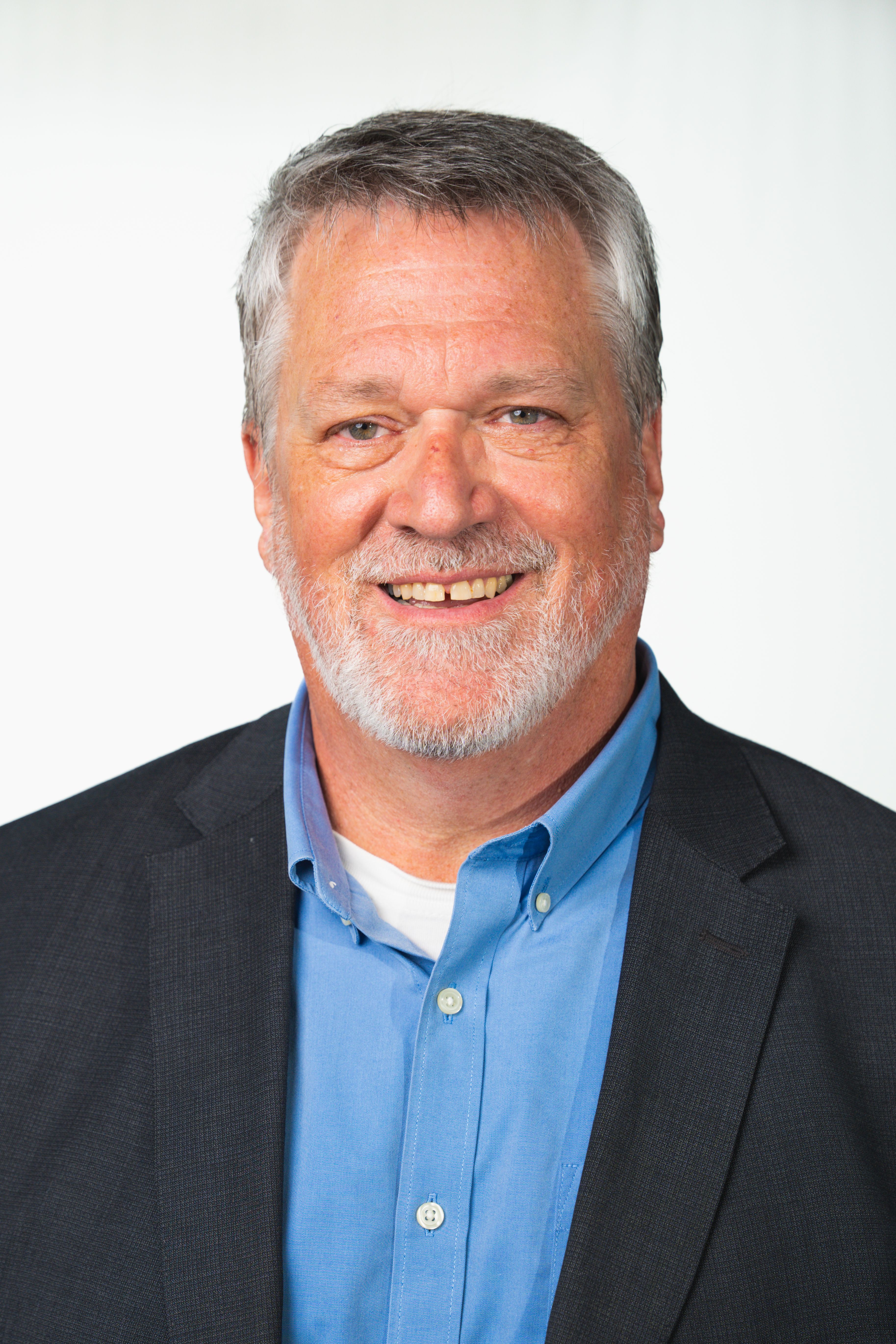