LED Lights Dominate TV-Film Industry
It’s the solid favorite, with a little room for improvement
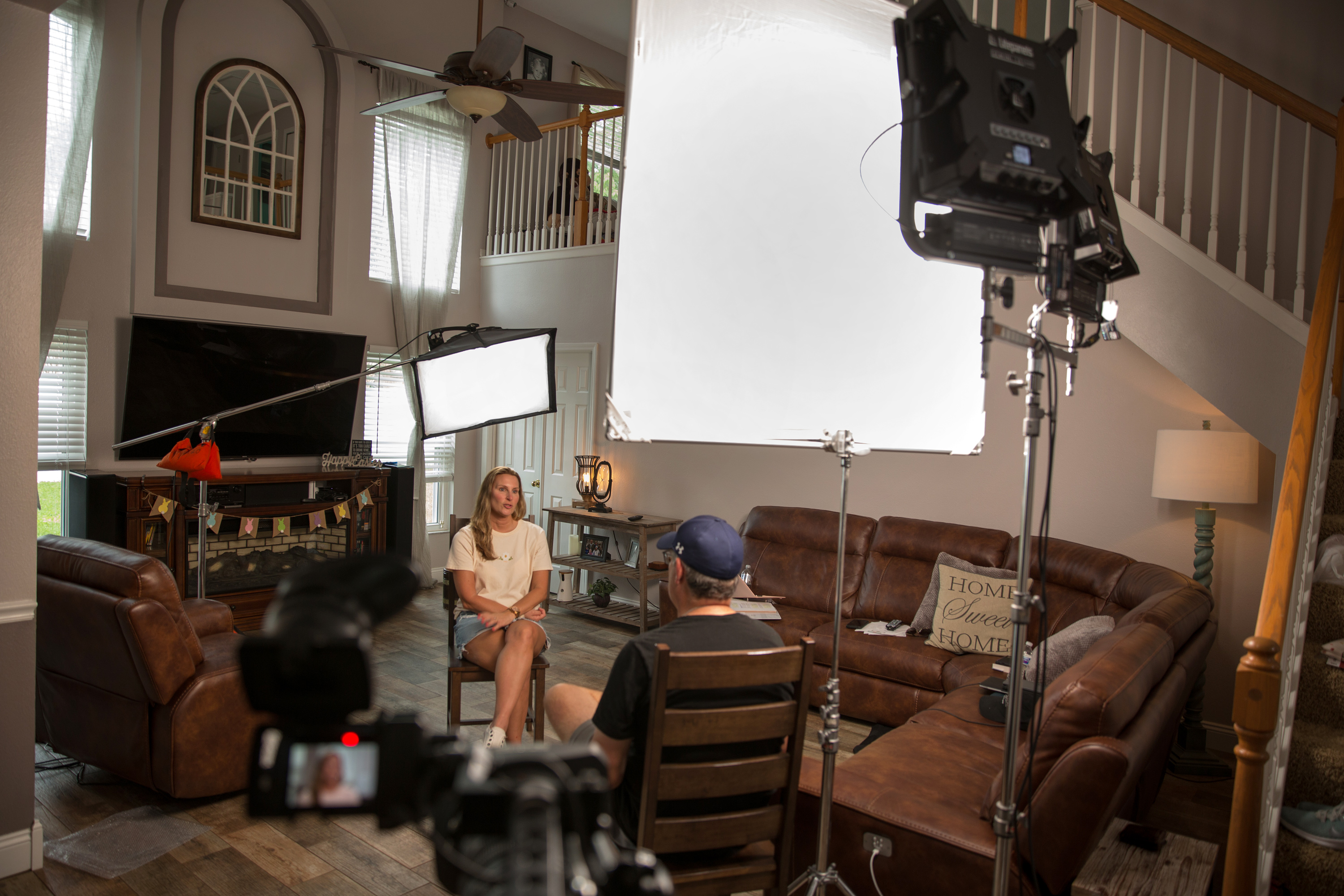
LEDs have revolutionized lighting in the past 15 years, and that is especially true for television lighting. Lightweight, compact, efficient, bright and cool, LED lights have kicked all other types of television lighting to the curb.
In addition to the LED light attributes already mentioned, there is one other benefit of LEDs that makes the technology seemingly ideal for television. LED’s components come in a wide range of shapes, sizes and emissivity, so they can be packaged in many different ways. Need lights on a car’s dashboard for an action shot? LEDs are the only choice that will fit the space, provide enough light, run all night from a simple battery and not bake your talent.
One other benefit of LED lights is that you can get devices that use red, green and blue LEDs, creating lights that can be adjusted to produce any color—and some pretty impressive lighting effects.
“The ability to produce any color from a light without gels is quite attractive, and using some number of color effects lights often makes a lot of sense,” said Pete Challenger, manager of U.S. sales and support for Lupo Lighting. “Whether it makes sense to use such lights for every fixture is more open to debate.”
LEDs were the overwhelming favorite of the companies contacted for this article, and the fact that LED lights can be configured in so many different ways is an important factor in their popularity.
Light Quality
One of the lingering questions about LED lighting is the quality of the light that the fixtures make. Tungsten incandescent lights made a broad spectrum of light that worked well with camera sensors. The first LED lights targeted at television production did not have this same quality of light.
Today, lights used in television are rated for their color rendering index, which is a measure of the light’s ability to reveal colors in the object illuminated by the light. The higher the number—up to 100—the better colors are represented.
Some early LED lights targeted for television production were rated at 75 CRI, while current technology is 95 CRI and higher.
“The first panels were rated about 70 CRI and tended to be rather green—but that didn’t stop people using them back then,” Challenger said. “Now if they don’t rate in the 90s, no one would consider them.”
Challenger said that Lupo’s latest Ultrapanel series of lights have lower- and higher-efficiency versions, and the lower-efficiency line has a CRI of 98, while the higher-efficiency model has a CRI of 96.
“Either of those would have been viewed as insanely good just a year or two back,” he said.
ENG Lighting
Frezzi has long made lights popular with ENG crews, combining small size, high durability and punchy brightness that makes on-camera talent stand out on murky city streets at night. The company’s tungsten and HMI lights got the job done a couple decades ago, but it is mostly all LED now.
“Our ENG customer’s primary application is live and in-the-field stand-ups, so they’re looking for the highest-output LED in a compact/lightweight form-factor,” said Kevin Crawford, vice president of engineering for Frezzi Energy Systems in Hawthorne, N.J. “Because our Frezzi SkyLight uses a single-source LED element, it provides a smooth, flat optical field with a single shadow and the intensity of an HMI in a user-friendly and small fixture.”
Are LED fixtures good enough to push HMI lights from the market, however?
“We also see the HMIs are being phased out rapidly for LEDs, even though they produce beautiful light,” Crawford said. “The product trend we see is for LEDs to replace tungsten and HMIs, as LEDs are becoming more efficient and continually improving in quality.”
Crawford said that LED is the light technology of the foreseeable future.
“LEDs are here to stay and always improving output, quality of light and efficiency,” he said. “HMIs have a much higher cost of operation/ownership, plus UV concerns, and lamp life is typically only 200 hours vs. 50,000 hours for LEDs. With new tunable LED single-source elements, we are mapping out adjustable color temperature fixtures [3200-5600K], while maintaining HMI-type output in a compact fixture.”
Form-Factor Finesse
LED lighting fixtures are available in many more shapes and designs than was possible with tungsten and HMI fixtures. One reason why is because of the high-efficiency/low-heat nature of LEDs—you can just package them in many different ways, and use a range of diffusing techniques to get the lighting effect you want.
“For LED fixtures, there are many different types of light modifiers now available, so end users can bounce and diffuse the light to change the size of the illuminated surface area, to get the desired result,” said Michael Herbert, product manager for Litepanels. “What is increasingly important is that the LED light itself has enough output to be used with a range of different modifiers.”
This is partially why Lietpanels is seeing a trend toward “hard” LED light sources, Herbert added.
“These high-output fixtures can throw beams of light through windows to simulate midday sunlight, but then can be pushed through multiple layers of diffusion to create a much softer lighting effect,” he said.
One benefit of LED lights is its excellent efficiency: They make a lot of light using a modest amount of power. Will this efficiency continue to improve over time?
“It has been increasing for many years, but we’re starting to see it level off,” Herbert said. “Unlike the general lighting industry, television and film lighting has to pay attention to the color quality of the LEDs. There’s an inverse relationship between color quality and LED efficiency—the more you focus on a broad, full-spectrum LED, the less efficient it’s going to be at converting electricity into light.”
How does the efficiency of LED lights compare with tungsten and HMI lights?
“Film lighting fixtures are now typically surpassing 100 lm/W, which is much more efficient than tungsten, but only about on a par with HMI,” Herbert said. “I think we will continue to see smaller, more incremental improvements in LED efficiency, but with an increasing focus on improving the color quality.”
White vs. Color
As is true for many technical situations, having flexibility is a good thing—if you understand how to use it and keep the parameters of the device in mind. Beginning several years ago, there was great interest in lights that had red, green, blue and white emitters; lights that could create light of any color and even produce effects like ambulance lights or mimic the light from a fireplace.
Such lights are still popular for many applications, and they can be the right thing for a range of applications. However, the key is that you need to understand what the light can do and how to get it to produce the light you need for your project.
“Just a couple of years ago everyone wanted RGBW lights, but in recent years the market has been asking for high-quality white light in fixed color temperature or in bi-color without RGB,” said Toby Sali, co-owner of BB&S Lighting. “What we hear from professionals is that the option to use RGB is not needed, and most of the time creates issues because of the option to add colors to the white light.”
Although LED components are generally stable, there is a little aging over time and slight variations among similar components.
“The problem with most RGBW fixtures is the calibration of the mixing of the different LEDs,” Sali said. “No LED is the same, and variations from diode-to-diode affect blending the RGBW colors to get the color temperature you want.”
A Match for Cameras?
So just how good are today’s LED lights? Ultimately, a camera has to capture the scene that the light is illuminating, so how well do today’s lights work with today’s cameras? Do tungsten lights still have an advantage in color purity?
“Matching tungsten really doesn’t matter much anymore in most cases,” Challenger said. “The issue is that all LED sources have non-continuous spectra— different manufacturers’ cameras have quite different spectral response, so it comes down to how the peaks and valleys of the LED spectrum align with camera sensors. My personal recommendation is, despite whatever color index is popular at the time, you should test lights you are considering by viewing the results through the cameras you have, or are considering. Anything else opens you up to the risk of unpleasant surprises.”
Frezzi’s Crawford said that modern lights and modern cameras are a good match.
“Today’s cameras can balance to all types of light sources,” he said. “The LEDs we use have a very good broadcast-quality spectrum, and our SkyLight is balanced at 5600K for maximum output to compete with a full-sun day. If tungsten color temperature is required for an indoor shoot, we have a flip-down converter filter that will balance to 3200K without significant loss of output.”
It may sound trite, but in the past 15 years, LED lights have revolutionized television lighting. In addition to being all the good things mentioned above (low-weight, low-heat, high-efficiency and available in a wide array of shapes and sizes), LED lights are also economical. They are no more expensive than the technologies that preceded them, and in many cases are less expensive.
Good-quality lights at common-sense prices is one more tool that the industry has used to drive down the cost of film/video production. It’s a win-win situation for creators—the gear keeps getting better, while the cost goes down.
It’s a great time to be creating content.
Get the TV Tech Newsletter
The professional video industry's #1 source for news, trends and product and tech information. Sign up below.
Bob Kovacs is the former Technology Editor for TV Tech and editor of Government Video. He is a long-time video engineer and writer, who now works as a video producer for a government agency. In 2020, Kovacs won several awards as the editor and co-producer of the short film "Rendezvous."