Applied Technology: Gepco's HD cable
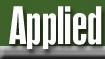
Gepco's HD cable
The frequency requirements for high-definition broadcasting far exceed those of any other video format. The good news is that as facilities begin to migrate to HD, they won’t have to worry about the transmission of less demanding formats such as analog or serial digital. In the past couple of years, connector and jack-field manufacturers have been busy making subtle changes and tweaking impedance in order to improve structural return loss, especially at frequencies from 1 to 3 GHz. For the most part, broadcast cable manufacturers have been ready for quite some time with products that meet HD requirements.
The mission for anyone making a video cable for HD is simple: manufacture a product that has no impedance variations over a broad frequency range.
How is this done? That’s where the simplicity ends. First, you need a center conductor that has no variations. Remember, impedance is determined by the diameter of the insulation over the diameter of the conductor. Conductor uniformity for solid wire is achieved by paying close attention during the drawing process to eliminate die chatter or scratching. This spurious phenomenon will cause multiple high-frequency structural return loss spikes.
Die chatter can create so many small spikes that, when viewed electrically on a spectrum analyzer, it looks as if it is some type of hash or noise instead of independent spikes. By looking closely under a microscope, one may observe what looks like randomly dispersed small divots in the wire. Upon even closer inspection with a measuring gradient in the microscope, a specific distance from one divot to the next can be observed. There are usually many groups of these periodically spaced grooves, and this is why they create so many structural return loss spikes.
Another method to ensure center conductor uniformity of the copper is to stop a couple mils short of the final required diameter at the intermediate drawing process, then draw the remaining two mils at the dielectric extrusion process. By using a clean precise diamond die to perform this single drawing operation, you can clean up many imperfections that were generated by previous drawing operations. This holds true as long as the imperfections do not exceed the depth of your final drawing operation. At worst, you will still reduce many anomalies and lower the structural return loss number at the higher frequencies.
Tension control is extremely important when manufacturing coaxial cable. A head is used to apply polyethylene. The consistency at which the plastic is applied is important. The control of periodicity at application of plastic is extremely important to reducing impedance variation of the final product.
Get the TV Tech Newsletter
The professional video industry's #1 source for news, trends and product and tech information. Sign up below.
Tension control systems usually consist of a motorized let-out system followed by an accumulation method integrated into a regenerative metering and take-up capstan, monitored through strain gages with a dampened method to adjust and hold a constant tension. Ensuring that the wire does not elongate over a long distance takes some very exacting equipment with the correct control algorithms to properly dampen the system so as not to overcorrect. Correct tension control not only can ensure the uniform application of the plastic, it also can maintain the exacting size of the wire, two extremely important requirements in manufacturing high-quality coaxial cable for HD.
In the manufacturing process, cable must pass over a series of guides in order to keep it properly aligned through its various paths from payoff to take-up. The wire, whether un-insulated or insulated, takes a route over guide wheels called sheaves, which have bearings at their center. In order to predict a potential problem with regard to periodicity it is best to, wherever possible, use sheaves and bearings that are the same size. This will ensure that when structural return spikes are discovered they may be easily traced back to a specific size sheave or bearing diameter.
To determine the diameter of a spurious sheave or bearing, simply convert the speed of the cable in feet per second, divide by the frequency of the spike in megahertz, multiply by 12 to convert to inches, and then divide by pi (3.1416) to get the diameter.
Coaxial cable anomalies can also be further reduced by the use of precision laboratory bearings. They are usually more costly and harder to find, but the results are worth the effort.
Creating foams is achieved by blending specific types of polyethylene. The recipe must be repeatable over a long time span for a broad product range, and the consistency of the compound must be maintained over a long duration.
Development process
Gepco’s development of a precision video cable for HD began back in 1986 with the introduction of VPM2000. This cable revolutionized wiring for the broadcast market due to its small size, low attenuation and ease of termination. Until its introduction, all precision cables for broadcast were constructed with solid polyethylene dielectrics. Velocity of propagation was restricted to 66 percent, shields were constructed of double braids and outer jackets were also solid polyethylene. All of which made for a product that was difficult to use, heavy, stiff and that did not meet any of the new UL requirements. Previous video broadcast cables had been modeled after the Western Electric 724 construction, the standard since the 1940s.
Up to this point, foam dielectrics were prohibitive for use as a precision coaxial product because of inconsistency in the blending of chemical foams, which caused variations in diameters, shrinkage and cracking with variations in temperatures.
With the development of nitrogen gas injection systems, creating foam for use as a dielectric with electrical consistency became practical. It made it possible to manufacture a product that could be regarded as precision. Blends of materials and delivery of the gas in the extrusion process now made foams harder and more consistent, with broader temperature operating range. Velocity of propagation rose to 82 percent, four percent better than chemical foam products.
Attenuations were much lower than any of the other precision cable available at the time. As broadcasters continue their migration into high definition and market demands continue to change, Gepco will also evolve its products to stay ahead of the market.
Gary R. Geppert is president, CEO and owner of Gepco International.