UPS & backup power systems
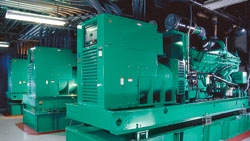
UPSs can be big, noisy and can certainly help warm a room, but they pale in comparison with the generator.
A generator is three-fourths of a locomotive, using the same diesel motors.
Emergency power systems usually consist of two components: a UPS and a generator. The UPS half of the system serves a couple of purposes. Online UPS will filter out power events that happen outside your facility — a necessity, as it is claimed that the average PC is subjected to more than a hundred power events per month. The second function is to provide power if main power ceases. On the average, the time a UPS is expected to do this is under five minutes — enough time to gracefully shut down equipment, and for the backup power generator to ramp up and take over the load.
UPS systems generate emergency power in one of two methods, either via batteries or with a flywheel that acts as a generator. Batteries can supply power for a longer period of time, but with increased cost in size, weight and maintenance. A typical UPS battery cabinet supporting a 100KW for a few minutes can weigh close to 3000lbs.
The flywheel approach uses mains to power a motor, which turns a flywheel. When mains power disappears, the flywheel acts as a generator for a short while due to built-up angular momentum — usually just long enough for the generator to power up and stabilize. A flywheel UPS is generally smaller than the battery versions.
Systems can be set as to how fast they will shed the load back onto the generator once it has come up to speed. If the UPS were to dump the entire load at once, the generator might stall or change frequency so drastically that the UPS would deem the power unstable and take the load back. Once the generator re-stabilized, the cycle could start again. UPS load relinquishing should be set to occur over a 20-second period. UPS systems also will slowly slew to the generator's frequency before shedding the load if that is different than the UPS's own frequency. This is especially important if there are motors as part of the load.
Generators
The professional video industry's #1 source for news, trends and product and tech information. Sign up below.
UPSs can be big, noisy and can certainly help warm a room, but they pale in these attributes compared to the other half of the emergency power system: the generator. A generator is three-fourths of a locomotive, using the same diesel motors, but lacking the traction motors to spin the wheels. Generator systems can weigh several tons. They also can have ear-splitting sound levels and parts that approach 2000 degrees. A 2MW generator will weigh more than 30,000 pounds and might need a 2000-gallon tank to fuel a 2900HP engine for a day and a half under full load. It could easily cost $400K.
Many generators have sound-baffling schemes that can lower the noise level, but baffling might affect cost. Whereas a non-sound damped unit might cost $150/KW, sound-damped units can be $225/KW. When turning air to dampen the sound, the unit tends to get bigger and will generally require more hardware. Absorption material also can help to quiet the unit, as does sealing it in a rigid enclosure. Adding a second enclosure around the first (double-walling) takes the level down further.
Like all engineering feats, generators are a series of tradeoffs. They are designed based on the engine driving them. Diesel engines produce more torque at lower RPMs than do gasoline engines. Generators coupled to diesel engines are designed to run at 1800rpm (60Hz AC output), while gas-driven generators run at 3600rpm.
Most modern generator construction consists of two major sub-components — a rotor and a stator. The rotor's core is a shaft with a number of poles. Each pole is essentially a long piece of iron around which is a coil of wire, forming an electromagnet. Electromagnets can produce more power per pound than permanent magnets. The stator surrounds the rotor assembly and is stationary.
Power is generated by a number of inductive steps. At one end of the rotor is a set of permanent magnets. The rotation of the rotor induces a small current into a stationary pilot exciter armature mounted on the stator. The output of this armature is rectified and feeds a stationary exciter-feed coil also mounted on the stator. The exciter-feed coil induces power into the rotating exciter armature on the rotor. This is rectified and fed to the main field coils wrapped around each pole. This forms the electromagnet mentioned before. These rotating poles induce power into three stationary main armatures on the stator, providing three-phase power out. Like everything else, the power out is not equal to the power in. Losses can be categorized: stray losses, friction and windage losses (mechanical), core losses, and I2R losses (copper losses).
Making a choice
There are several choices that will have to be made when selecting a generator. The size of the unit will depend on the use. Most content providers use generators as standby units. They provide power to a varying load for the duration of the normal source of power. Providers recommend that they be sized initially for 60 percent of the actual load because loads tend to increase over the average 30-year life of the unit.
Television stations seem to forget about studio lights when computing the load. A San Francisco O&O was recently hit with a rolling blackout in the middle of its evening newscast. Everything appeared to be generator-supplied except studio lights. The next segment of the newscast was done with talent holding flashlights under their chins. The effect was interesting, if unflattering, for the people holding the flashlights. Even if you only supply studio work lights under generator operation, the event would go more smoothly than the flashlight approach.
Sizing the generator to match the load is important. If the load is too high, excessive piston loading can occur along with high exhaust temperatures. Conversely, generators that are underloaded can have governor problems (called “engine slobber” by the industry).
A note here about getting the experts involved early: Your generator vendor and contractor should meet to ensure that generator issues are properly addressed. There are often several regulatory agencies that you must deal with when installing a generator. For example, many areas have air-quality control districts. Besides emission requirements they often have restrictions as to how many hours the generator can be run per year; 200 hours is a common limit. Consultation by the knowledgeable parties can keep you from running afoul of local regulations.
Other considerations
The fire officials should be contacted. In many locales, they issue the fuel permits required to install the needed fuel tanks. Also, most counties or cities have sound restrictions. Where the generator is installed can impact the sound reduction techniques that are required. If the generator is to be installed inside a building, the building codes in your area will most likely come into the mix.
Keep in mind that standby units must be exercised regularly. Standby engines/generators that cannot be loaded should only be run long enough to achieve normal oil pressure and then shut down (generally under five minutes). The unit must have adequate clean, cool air for cooling and combustion. Exhaust ducting should be thermal wrapped to minimize heat buildup in the room housing the generator. The exhaust stack and muffler must be of sufficient size to keep exhaust back pressure in spec. Excessive back pressure will raise exhaust temperature and reduce engine life.
Vibration is another factor. Many generator vendors have precise specifications as to the concrete pad or base that the generator sits on. Although generators aren't excessively vibratile, when placed in a larger structure a component of the overall vibration energy could become resonant. While usually not damaging to the generator, it could cause problems in the areas around it. Your vendor and contractor should help determine what isolation is required for your particular installation. In areas where earthquakes are a possibility, special seismic restraining or damping devices must be used. A strong earthquake could impart enough movement into the unit to damage it or have it come off its mounts. Vibration isolators also can reduce noise levels.
A few months ago, most of us thought that an unstable electric power supply was a specter only affecting people who continually worry whether the sky is falling. Considering what we've learned from California — a lesson others across the country might soon share — the worriers were right. Anyone responsible for keeping a television facility on the air should move emergency power to the top of the list of issues.
Jim Boston is director of emerging technology for The Evers Group.