Streamlining broadcast operations
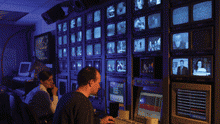
At Real Broadcast Network’s all-digital Internet Broadcast Operations Center (IBOC) in Seattle, employees operate an event management system for proprietary traffic and billing.
During the first few decades of broadcasting, stations devised the processes, acquired the tools and justified the staffing to deliver programming to the viewer. Television borrowed some methods from the more mature radio industry. But without a mature business model to implement, it followed a more extemporaneous path. The hardware from those early days has been updated by generations of new technology. But, unfortunately, many of the oldest manual tasks and operational processes from those days have perpetuated and are alive and well in many of today’s TV stations.
Automation
Today, program automation is common in many television facilities, primarily to reduce operational costs. But few, if any, broadcast stations use automation for its designed purpose: unattended master-control operation. The reasons for this are not fully understood, but there are at least two contributing factors. First, for many decades, FCC rules mandated that someone be present to monitor the transmitter signal. Second, stations have been reticent to leave their playback systems unattended because many manual data processes within the station lack robustness and error checking, and can corrupt the data being delivered to the automation server.
Automated stations still require an operator in master control working as a backup to the system. The operator’s primary functions are to perform quality control on the program stream, correct the program playlist and manually switch program elements that are not automated. Finally, the MC operator is there to help prevent catastrophic failure in the program streams.
Another issue with today’s automation technology is that functions are still performed repeatedly, often by a different department within the same station. Let’s look at two examples.
One primary duty of the MC operator is to provide a quality control check over video feeds as they are recorded. The operator repeats this function again when the station finally airs the program. A second, and more labor-wasting, example involves logs. The traffic department creates program logs and then delivers them to master control. The MC operator then changes and corrects the logs to represent the actual as-aired program conditions. Similar procedures are common throughout a typical station’s operation. Think of the efficiencies and error reductions the station might enjoy if it automated some of these processes, or at least, handled them only once.
Get the TV Tech Newsletter
The professional video industry's #1 source for news, trends and product and tech information. Sign up below.
The need to do things differently
Today, stations still perform many operations based on equipment and conditions originated in the 1950s and 1960s. Paper logs are still common. People still handle last-minute changes by telephone or notes passed between traffic and operations or engineering.
Technology has improved, and stations can now manage log data electronically. Yet several station personnel often process the same data, which increases the opportunity for errors. The result is that, for the sake of expediency, stations often improvise impromptu, ad hoc solutions – Band-Aid – to fix operational problems that are systemic in nature. And, after a while, Band-Aids begin to cover Band-Aids. Occasionally, the process even repeats itself.
Nearly all broadcast stations use the Band-Aid approach. Fortunately, methods exist to cleanse business operations and monitor future modifications. Put another way, there are tools that stations can use to eliminate many of the Band-Aids. These methods and tools are part of a reorganization process that can put the station back on track. Let’s take a look at how it works.
Reorganization
First, the reorganization requires that stations identify and eliminate repetitious tasks. Obsolete processes and historical fixes are easy to identify on a flow chart. Unfortunately, replacing a multi-task process can be difficult. It might be necessary to hire a consultant to review a station’s operations, searching for processes that can be automated or eliminated altogether.
Generally, the goals of such a review are to:
- make the operation as linear as possible
- emphasize electronic data over paper data
- reduce or eliminate multiple data entry
- automate where cost-effective
- eliminate obsolete tasks
- logically reassign task responsibilities to improve data flow and task accuracy
In addition, every proposed change must go through a cost/benefit analysis. The goal is not to replace people with machines but to maximize staff creativity and productivity. Many times, the long-term cost of staff is less than that of an automation system or optical fiber link. Don’t enter the process with the idea that you’re simply going to replace people with equipment. That’s not the solution.
Analyzing broadcast operations
The process of reorganizing station operations is not trivial. In fact, it may take as long as a year. Choosing a person or company to perform the station operational analysis takes careful consideration. Bringing in a third party for a thorough station analysis is a big step, not to be taken lightly. The consultant must possess a thorough working knowledge of operations in traffic, master control, promotion, news, program services and sales. Although in-house staff may be competent in these areas, an outside analyst has the advantage of a fresh perspective. As stations progress into the 21st century, they need to re-examine their workflow with an experienced operations analyst. The goal is to improve operations and efficiently while enabling the staff to be more creative and productive.
The first phase of the consultant’s job involves analyzing the current operation and understanding the current business environment. Secondly, the consultant needs to understand the station management’s long-range goals. It’s important that the consultant know, for example, if the station plans to double the amount of newscasts over two years. If your station doesn’t have a long-range plan, you’ll have to get one in place before the consultant can effectively begin the process.
The first step in understanding how a station works is to make a thorough audit of the various operational areas. The audit process begins with interviews of both staff and management. It generally takes two to three days to complete this process. A small-market station may require only a single day.
All employees with information about any operational area are interviewed. This includes almost everyone. In large departments, or in those working multiple shifts, the auditors must interview even those employees on different shifts or days of the work week. Often, there are operational differences among day, night and weekend periods, and differences between the duties of full-time and part-time workers.
The general manager, controller and general sales manager need to provide information about labor contracts, niche operations or areas that are important profit centers for the station, policies dictated by ownership that may constrain reorganization, and other market-specific issues the station faces.
While there are several methods the station can use to uncover all this information, two methods are common. The first is to inventory each of the tasks performed by each employee. Supervisors go through a list of employees and catalog all of the tasks each employee performs on a routine basis. They also catalog estimates of employee time spent on each task, volume of output, critical timelines, error rates, tools used, etc. It is important to note the error-detection process or feedback to the employee during task performance. The consultant is critical here as an independent observer. Often, the front-line staff is so familiar with how they work that they will leave out critical steps they perform — omissions that an outsider will catch.
A second approach to the operational analysis is to follow the data paths throughout the station and learn the processes that follow. Data paths are all of the data that pass through a station, such as the ordering process for commercial spots, programming schedules from station management, program timing information, and upcoming news stories being readied for the newscast’s final rundown. An interviewer asks each department to identify all of the sources of data coming into the department and what forms the data take — paper, electronic, word of mouth, faxes, videotapes, etc.
Using the list of data sources, the interviewer then asks what tasks within the work area use each datastream, what changes are made to the data, and what data leave the department as a result of processing. Information is catalogued relating to who gets the outputted data, what form the data takes, critical timelines, error rates and any feedback loops that exist.
This method is extremely helpful in understanding exactly what people do, who is impacted and whether the process has Band-Aids already in place. This method checks well because the manager can provide information relating to the overall work area while employees can confirm the manager’s account and add details not generally known to the manager. Another useful aspect of this method is the ability to track data across department lines.
The data-collection process must be detailed, so it becomes an iterative process, with the analyst graphing operational data, reviewing the data with management, and then correcting the graphical representations before entering the next phase.
Near the end of the data-acquisition process, the analyst assembles the paper data from the station. This would include program logs, satellite-record schedules, spot-dub requests, work schedules, news-assignment logs, graphics requests, promotion-tagging data and other written information commonly sent throughout the station. These data are used to confirm or establish the volumes of workflow. This is where W-2 information, work schedules and operational budgets are used to analyze the real cost of current operations. Later, the analyst will use this same information to evaluate the costs of various operational models.
The flow chart
Armed with the defined tasks and processes from the interviews and the paper trail from hard copy records, the analyst begins to create a flow chart that describes the whole station operation.
A task flow chart for a typical station should look like a funnel with its large end on the left and the spout on the right. The left side of the chart (the large end of the funnel) represents the input of many diverse streams of data entering the station. These could be spot orders, program information, satellite feeds or news content. To the right, the few lines leaving represent the station’s program stream, client billing and FCC reports.
If the station is operationally efficient, it will process this data in a linear manner and the chart will show multiple data streams merging into fewer and fewer data paths as the lines move to the right. Bulges in the chart represent the Band-Aids mentioned earlier. These inefficient operations appear as long paths with numerous tasks and few data lines entering or leaving the path. The number of manual tasks performed on automation input and output data is a measure of the station’s automation efficiency.
The hard part
Now comes the really hard part. The analyst must develop a recommended operating model for the station and a transition plan that ensures a smooth reorganization. The analyst must be extremely careful in making recommendations for reorganization. The proper new model can only be designed if the analyst fully understands the consequences of each and every element of change he recommends.
Larry Brandt is a senior broadcast engineer with Digital System Technology.